Introuction
The two most common types of custom-made gaskets are molded gaskets and CNC-made gaskets. Both options provide a cost-effective solution for high-volume production.
Molded gaskets require specialized equipment, which can have an initial cost ranging from 20,000 to 50,000 GBP to start production. On the other hand, CNC gaskets offer competitive pricing even for small quantities of gaskets needed. While molded gaskets can be manufactured in any shape required, CNC-made gaskets are limited to flat materials.
In this article, we will delve into the most common uses and sourcing methods for custom-made gaskets for both private and business buyers.
Gaskets are essential components in a multitude of mechanical systems, serving the critical function of sealing interfaces between two or more surfaces. Their primary purpose is to prevent leakage of fluids or gases, ensuring the efficient and safe operation of various machines and equipment. Gaskets are ubiquitous, found in everything from automobile engines and pipelines to hydraulic systems and aerospace applications. The effectiveness of a gasket hinges on several factors, including the material from which it is made, its design, and the precision with which it is manufactured. In recent years, Computer Numerical Control (CNC) machining has emerged as a dominant technology for gasket production, offering unparalleled accuracy, repeatability, and versatility compared to traditional manufacturing methods. This document provides a comprehensive overview of CNC-made gaskets from flat materials, exploring the process, materials, advantages, applications, and considerations for optimal gasket performance.
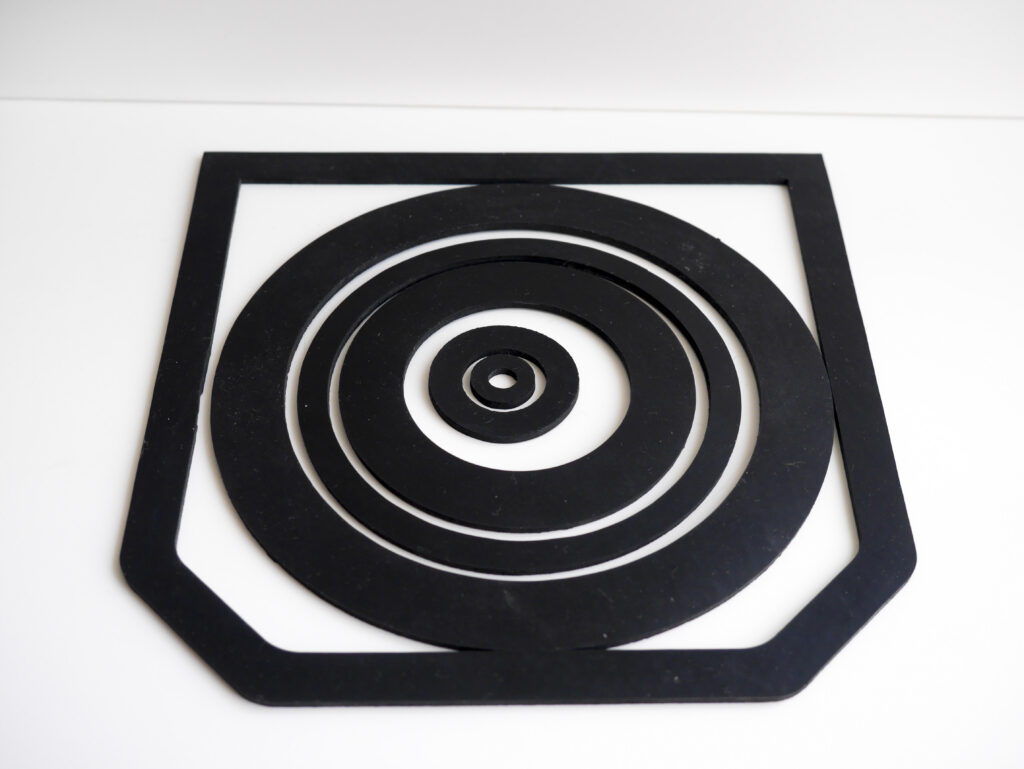
Sourcing your gaskets
There are numerous professional companies in the market that provide CNC gasket cutting services, offering high precision and a wide variety of materials. One such company is CS Made, which can be found at https://csmade.co.uk/ (CSMADE)
The importance of gaskets
Before delving into the intricacies of CNC gasket manufacturing, it is crucial to understand the significance of gaskets in various industries. Gaskets are not merely passive components; they are integral to the reliable functioning of countless systems. Consider the following points:
Preventing Leakage:
This is arguably the most fundamental role of a gasket. Leakage can lead to loss of valuable fluids or gases, environmental contamination, and compromised system performance. For instance, in an internal combustion engine, a leaking head gasket can result in a loss of compression, leading to reduced power output and potential engine damage.
Maintaining Pressure:
In pressurized systems, gaskets are essential for maintaining the desired pressure levels. Leakage can cause pressure drops, leading to inefficiencies and potentially dangerous situations. This is particularly critical in hydraulic and pneumatic systems.
Sealing against Contaminants:
Gaskets can also prevent the ingress of contaminants, such as dirt, dust, and moisture, into sensitive areas of a system. This is especially important in applications where cleanliness and purity are paramount, such as in the pharmaceutical and food processing industries.
Dampening Vibration and Noise:
In certain applications, gaskets can also serve to dampen vibration and noise. This is achieved by using gaskets made from resilient materials that absorb energy and reduce the transmission of vibrations.
Compensation for Surface Irregularities:
Even carefully machined surfaces may have microscopic irregularities. Gaskets can conform to these irregularities, creating a tight seal even when the mating surfaces are not perfectly smooth. The consequences of gasket failure can range from minor inconveniences to catastrophic system failures. Therefore, selecting the right gasket material and ensuring precise manufacturing are of paramount importance.
CNC Machining for Gasket Production
CNC machining is a subtractive manufacturing process that uses computer-controlled machine tools to remove material from a workpiece, gradually shaping it into the desired form. In the context of gasket production, CNC machining offers several distinct advantages over traditional methods like stamping or die-cutting.
Accuracy and Precision:
CNC machines can hold extremely tight tolerances, often within a few thousandths of an inch. This level of precision is critical for ensuring that the gasket conforms perfectly to the mating surfaces and creates a reliable seal. Precise cuts minimize material waste and ensure consistent performance across multiple gaskets.
Repeatability:
Once a CNC program is created and verified, it can be used to produce identical gaskets repeatedly. This is essential for mass production and ensures that all gaskets meet the required specifications. This consistency is difficult to achieve with manual methods.
Complex Geometries:
CNC machining can easily produce gaskets with complex geometries, including intricate shapes, tight radii, and small features. This is particularly important for applications where standard gasket shapes are not suitable. Internal cutouts and complex profiles are easily achieved with CNC.
Material Versatility:
CNC machines can work with a wide range of materials, including elastomers, plastics, metals, and composites. This allows manufacturers to choose the optimal material for each specific application, considering factors such as temperature, pressure, chemical compatibility, and cost.
Reduced Tooling Costs:
Compared to stamping or die-cutting, CNC machining typically requires less expensive tooling. This is because the same cutting tools can be used to produce a variety of gasket shapes, simply by changing the CNC program.
Rapid Prototyping:
CNC machining is ideal for rapid prototyping. Design changes can be quickly implemented in the CNC program, and new gasket prototypes can be produced in a matter of hours. This allows engineers to iterate on designs and optimize gasket performance before committing to mass production.
Minimal Material Waste:
Optimized CNC programming and nesting strategies can minimize material waste during gasket production. This is not only cost-effective but also environmentally responsible.
The CNC Gasket Manufacturing Process
The CNC gasket manufacturing process typically involves the following steps:
1. Design:
The first step is to create a digital design of the gasket using Computer-Aided Design (CAD) software. This design specifies the gasket’s dimensions, shape, and any other relevant features.
2. Material Selection:
Based on the application requirements, the appropriate gasket material is selected. Factors to consider include temperature, pressure, chemical compatibility, and cost.
3. CNC Programming:
The CAD design is then converted into a CNC program using Computer-Aided Manufacturing (CAM) software. The CNC program instructs the CNC machine on how to move the cutting tools to create the desired gasket shape. This program defines the toolpath, cutting speeds, and other machining parameters.
4. Material Preparation:
The selected material is prepared for machining. This may involve cutting the material to the appropriate size and shape or securing it to the CNC machine table.
5. CNC Machining:
The CNC program is loaded into the CNC machine, and the machining process begins. The cutting tools remove material from the workpiece, gradually shaping it into the final gasket form.
6. Quality Control:
After machining, the gasket is inspected to ensure that it meets the required specifications. This may involve visual inspection, dimensional measurements, and other quality control tests.
7. Finishing (Optional):
Depending on the application, the gasket may undergo additional finishing operations, such as deburring, cleaning, or coating.
Materials Used for CNC-Made Gaskets
The choice of gasket material is crucial for ensuring optimal performance. A wide range of materials can be used for CNC-made gaskets, each with its own unique properties and characteristics. Common gasket materials include:
Elastomers (Rubber):
Elastomers are widely used for gaskets due to their flexibility, resilience, and ability to conform to surface irregularities. Rubber and silicone gaskets at low prices – Custom Made – are specialists in rubber gaskets. Common elastomers include:
Nitrile Rubber (NBR):
NBR is known for its excellent resistance to oils, fuels, and solvents. It is a common choice for automotive and industrial applications.
Ethylene Propylene Diene Monomer (EPDM):
EPDM offers excellent resistance to weathering, ozone, and UV radiation. It is often used in outdoor applications.
Silicone Rubber:
Silicone rubber is known for its high-temperature resistance and excellent flexibility. It is often used in food processing and medical applications.
Silicone gaskets – Custom Made
Fluorocarbon Rubber (Viton):
Viton offers exceptional resistance to chemicals, high temperatures, and fuels. It is often used in aerospace and chemical processing applications.
Plastics:
Plastics offer a combination of strength, stiffness, and chemical resistance. Common plastics used for gaskets include:
Polytetrafluoroethylene (PTFE):
PTFE is known for its exceptional chemical resistance, low friction, and high-temperature resistance. It is often used in corrosive environments.
Polyethylene (PE):
PE is a versatile and cost-effective plastic with good chemical resistance.
Polypropylene (PP):
PP offers good chemical resistance and is commonly used in food packaging applications.
Polyvinyl Chloride (PVC):
PVC is a durable and versatile plastic with good chemical resistance.
Applications of CNC-Made Gaskets
CNC-made gaskets are used in a wide range of applications across various industries. Some common applications include:
Automotive:
Engine gaskets, exhaust gaskets, transmission gaskets, and oil pan gaskets.
Aerospace:
Sealing components in aircraft engines, hydraulic systems, and fuel systems.
Industrial:
Pipeline gaskets, pump gaskets, valve gaskets, and heat exchanger gaskets.
Medical:
Sealing components in medical devices and equipment.
Food Processing:
Sealing components in food processing equipment.
Electronics:
Sealing enclosures for electronic devices.
Hydraulics and Pneumatics:
Sealing cylinders, valves, and fittings.
Oil and Gas:
Sealing pipelines, valves, and wellhead equipment.
Considerations for Optimal Gasket Performance
To ensure optimal gasket performance, several factors must be considered:
Material Compatibility:
The gasket material must be compatible with the fluids or gases that it will be sealing.
Temperature Range:
The gasket material must be able to withstand the operating temperature range of the application.
Pressure Rating:
The gasket must be able to withstand the operating pressure of the application.
Surface Finish:
The mating surfaces must have a suitable surface finish to ensure a proper seal.
Gasket Installation:
The gasket must be installed correctly, with the appropriate torque applied to the fasteners.
Gasket Design:
The gasket design must be appropriate for the application, considering factors such as the shape of the mating surfaces and the type of fluid or gas being sealed.
Tightening Sequence:
Using the proper tightening sequence for bolts or screws is critical to distribute pressure evenly across the gasket and ensure a proper seal.
Conclusion
CNC machining has revolutionized gasket manufacturing, offering unparalleled accuracy, repeatability, and versatility. CNC-made gaskets from flat materials are used in a wide range of applications across various industries, providing reliable sealing solutions for critical systems. By carefully considering material selection, design, and installation procedures, engineers and manufacturers can ensure that CNC-made gaskets perform optimally and contribute to the safe and efficient operation of their equipment. The continued advancement of CNC technology and materials science will undoubtedly lead to even more sophisticated and reliable gasket solutions in the future.