Silicone gaskets are widely used across industries due to their flexibility, durability, and excellent sealing properties. Whether in automotive, food processing, or electronics, silicone gaskets offer a reliable sealing solution. However, like any material, silicone has its pros and cons. In this article, we’ll break down the advantages and disadvantages of silicone gaskets to help you make an informed decision.
What Are Silicone Gaskets? 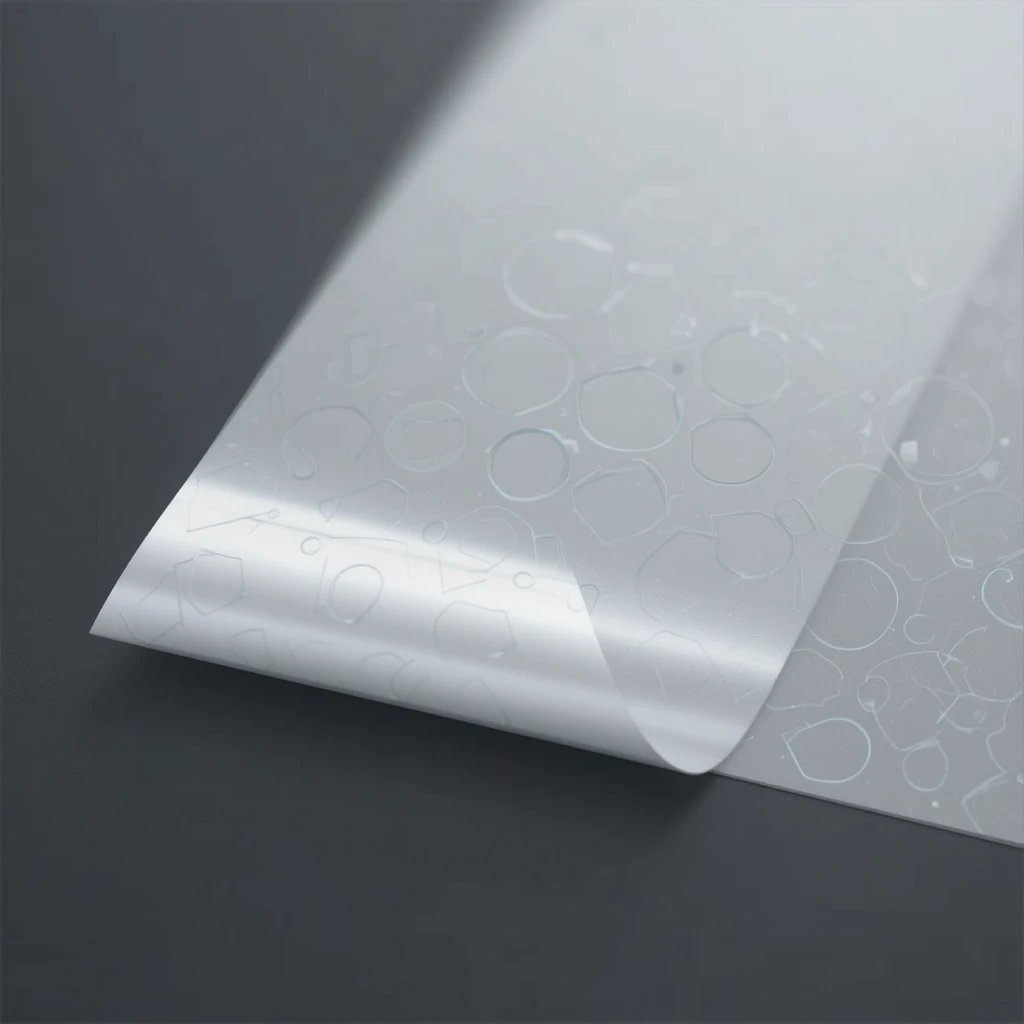
Silicone gaskets are mechanical seals made from silicone rubber. Known for their thermal stability, chemical resistance, and flexibility, they are ideal for applications requiring airtight or watertight seals in extreme environments.
Advantages of Silicone Gaskets 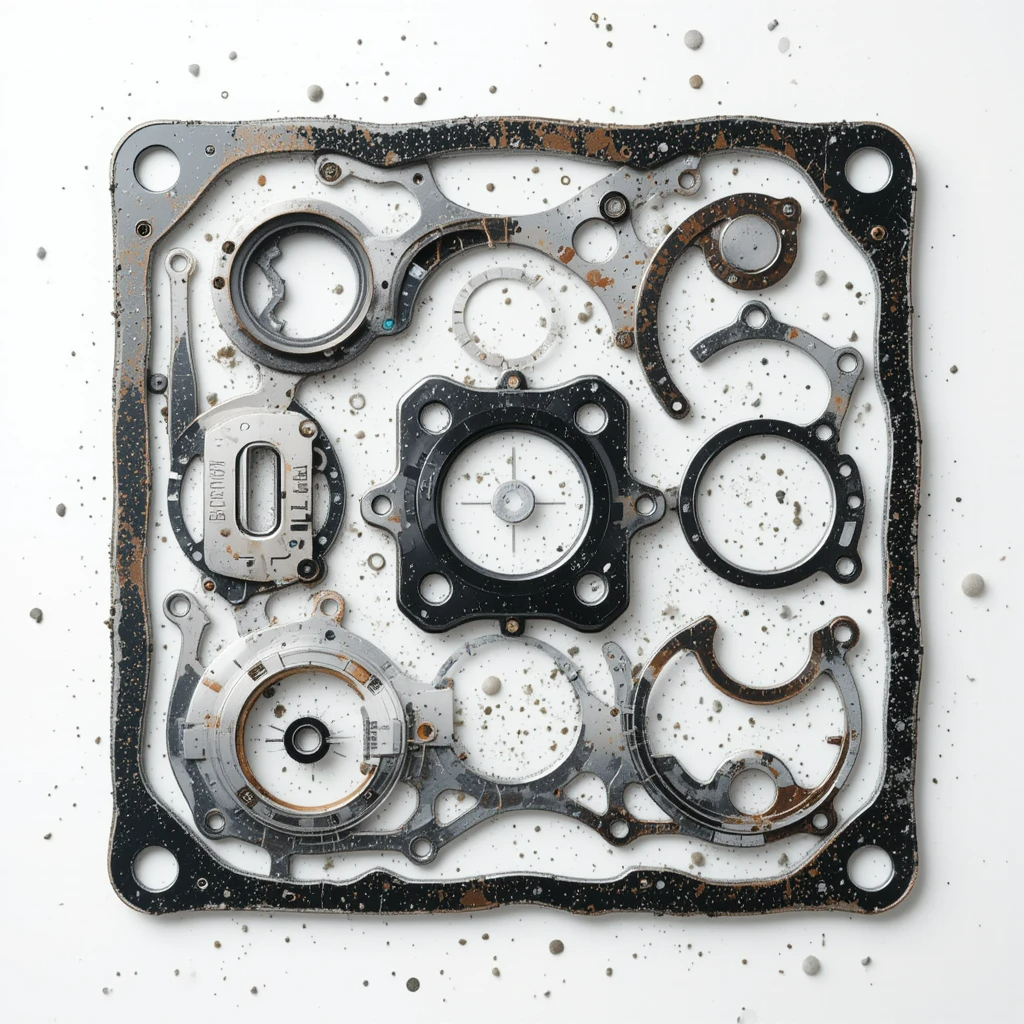
1. High Temperature Resistance
Silicone gaskets can withstand extreme temperatures, typically ranging from -60°C to 230°C (-76°F to 446°F). Some specialty grades can go even higher, making them perfect for high-temperature applications.
2. Excellent Weather and UV Resistance
Silicone is naturally resistant to ozone, sunlight (UV), and weathering, making these gaskets ideal for outdoor use and long-term durability.
3. Superior Flexibility and Elasticity
Even after prolonged use, silicone gaskets maintain their elastic properties, ensuring consistent sealing performance over time.
4. Non-Toxic and Food-Grade Options
Many silicone gaskets are FDA-approved and safe for food and medical applications, which is why they are commonly used in the pharmaceutical, food processing, and beverage industries.
5. Chemical Resistance
Silicone is resistant to many chemicals, oils, and solvents, which is especially useful in industrial and automotive environments.
6. Low Compression Set
Silicone gaskets retain their shape and sealing ability even after long periods of compression, reducing the risk of leakage.
Disadvantages of Silicone Gaskets 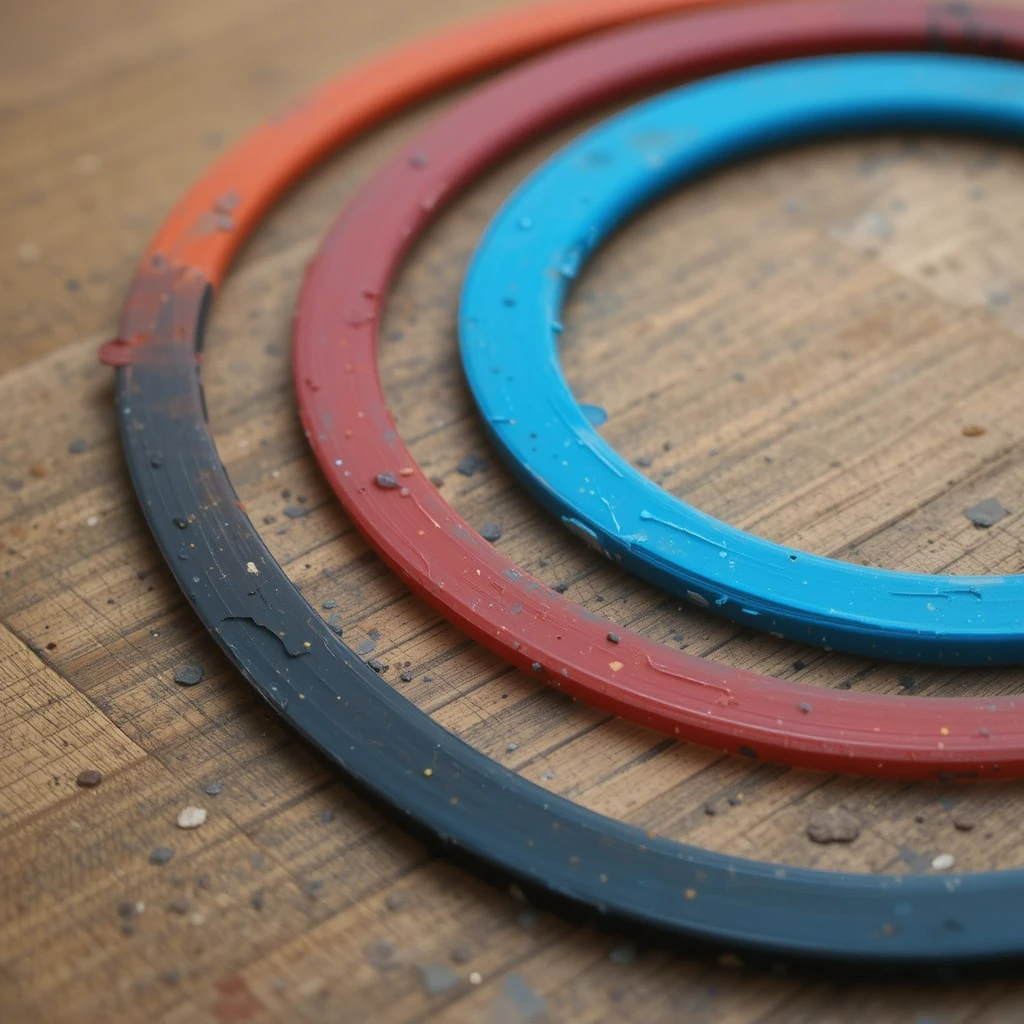
1. Higher Cost
Compared to other materials like nitrile or neoprene, silicone gaskets tend to be more expensive, both in raw material and manufacturing costs.
2. Limited Abrasion Resistance
Silicone is not ideal for high-friction or abrasive environments, as it can wear down faster than other rubber materials.
3. Low Tear Strength
Although flexible, silicone can be prone to tearing under mechanical stress, especially if not properly installed or if subjected to frequent flexing.
4. Poor Resistance to Certain Chemicals
Silicone is not resistant to all chemicals, including some acids, alkalis, and petroleum-based fluids. This limits its use in certain chemical processing applications.
5. Limited Electrical Conductivity
While silicone offers excellent insulation, conductive silicone is required for EMI shielding or grounding, which adds to cost and complexity.
Is a Silicone Gasket Right for Your Application? 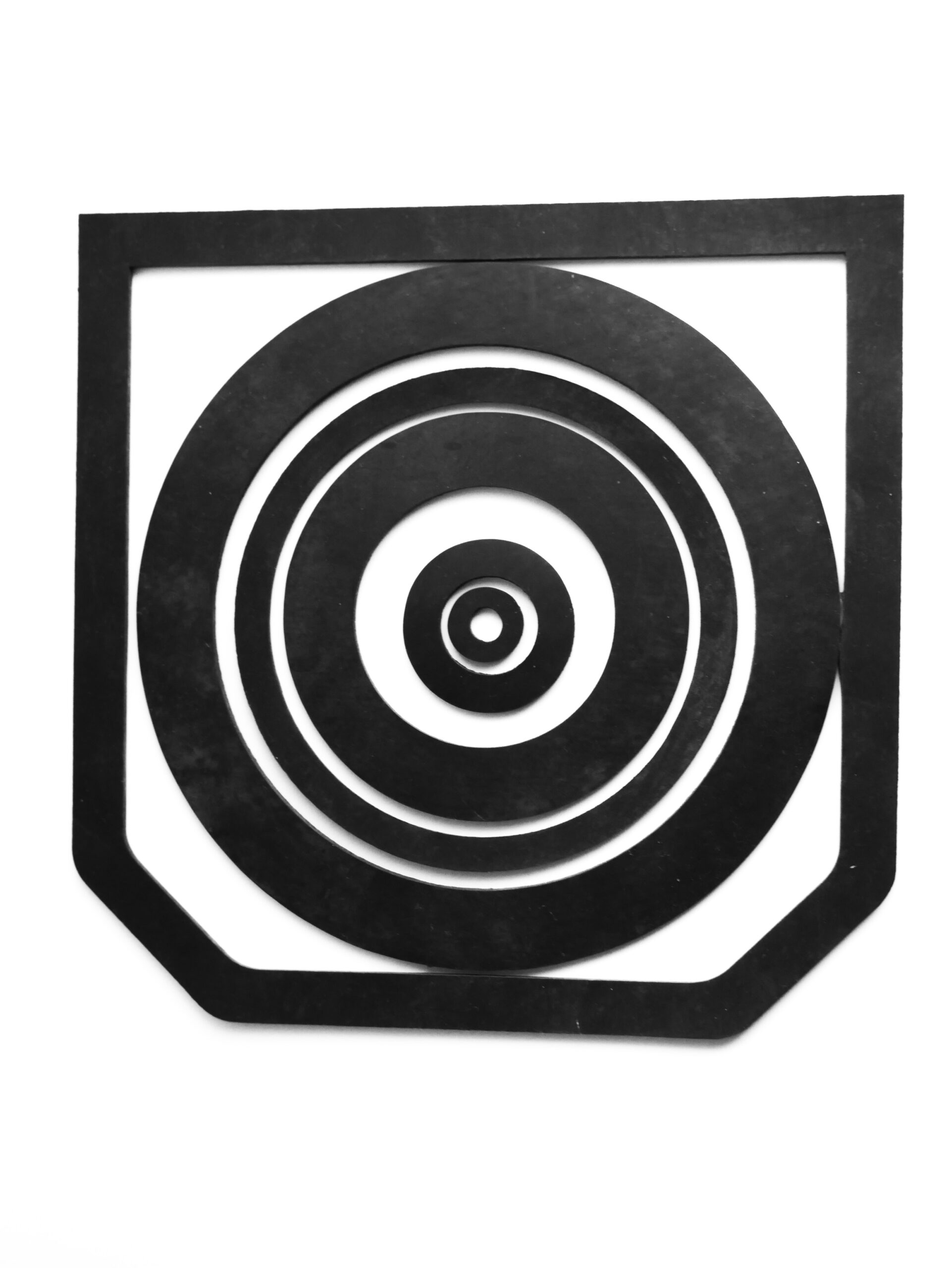
Silicone gaskets are an excellent choice for applications that require:
- High and low temperature performance
- Flexibility and long-term durability
- Resistance to UV, ozone, and weather
- Food or medical-grade materials
However, if your application involves abrasion, high mechanical stress, or exposure to petroleum-based chemicals, you may want to consider alternative materials like EPDM, Viton®, or nitrile rubber.
Conclusion
Silicone gaskets offer a unique combination of thermal stability, flexibility, and chemical resistance, making them a preferred choice for many demanding applications. However, understanding their limitations is crucial to avoid failure and unnecessary costs.
When choosing a gasket material, always consider the environmental conditions, mechanical requirements, and industry standards of your application.