Introduction
EPDM (ethylene propylene diene monomer) gaskets are widely employed in various industrial applications due to their excellent sealing properties, durability, and resistance to environmental factors. A critical parameter in ensuring the optimal performance of these gaskets is the compression percentage. This refers to the extent to which the gasket is compressed during installation, influencing its ability to create and maintain a tight seal. Understanding and controlling the compression percentage of EPDM gaskets is essential for preventing leaks, ensuring system integrity, and maximizing the lifespan of the gasket.
Understanding Compression Percentage
Compression percentage is defined as the ratio of the amount the gasket is compressed to its original thickness, expressed as a percentage. The formula for calculating compression percentage is:
Compression Percentage = [(Original Thickness – Compressed Thickness) / Original Thickness] x 100 For example, if an EPDM gasket with an original thickness of 5mm is compressed to a thickness of 3mm during installation, the compression percentage would be:
Compression Percentage = [(5mm – 3mm) / 5mm] x 100 = 40%
The optimal compression percentage for EPDM gaskets typically falls within a specific range, as recommended by the gasket manufacturer or industry standards. This range is determined by factors such as the specific EPDM compound, gasket design, application conditions, and the desired sealing performance.
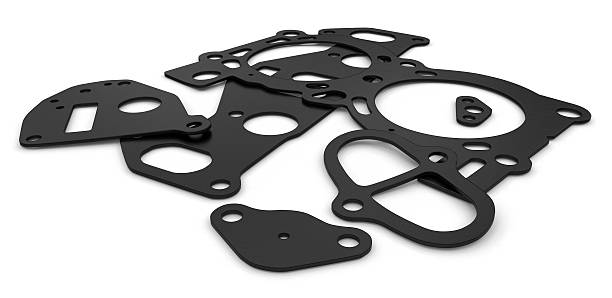
Importance of Proper Compression
Achieving the correct compression percentage is crucial for the following reasons:
1. **Sealing Performance:** Adequate compression is necessary to create a tight seal between the mating surfaces. When compressed, the EPDM material conforms to the surface irregularities, filling any gaps and preventing leakage of fluids or gases. Insufficient compression may result in a compromised seal, leading to leaks and potential system failures.
2. **Stress Relaxation:** EPDM, like other elastomeric materials, exhibits stress relaxation over time, which means that the compressive force exerted by the gasket gradually decreases. Proper initial compression helps to compensate for this relaxation, ensuring that the gasket maintains sufficient sealing force throughout its service life.
3. **Gasket Lifespan:** Over-compression can damage the EPDM material, leading to premature failure. Excessive compression can cause the gasket to deform permanently, lose its elasticity, and become more susceptible to cracking or tearing. Under-compression, on the other hand, may result in a loose seal and increased risk of leaks, which can also shorten the gasket’s lifespan.
4. **Application-Specific Requirements:** Different applications may require different compression percentages based on factors such as pressure, temperature, and the type of fluid or gas being sealed. For example, high-pressure applications typically require higher compression to ensure a robust seal.
Factors Influencing Optimal Compression Percentage
Several factors influence the optimal compression percentage for EPDM gaskets:
1. **EPDM Compound:** Different EPDM compounds have varying hardness, elasticity, and compression set properties. The optimal compression percentage should be determined based on the specific compound used in the gasket.
2. **Gasket Design:** The geometry and dimensions of the gasket, including its thickness, width, and shape, can affect the required compression percentage. Gaskets with complex designs may require more careful consideration to ensure uniform compression across the sealing surface.
3. **Mating Surface Finish:** The surface finish of the mating flanges or components can influence the required compression. Rougher surfaces may require higher compression to ensure that the gasket fills all the irregularities and creates a tight seal.
4. **Temperature:** Temperature variations can affect the elasticity and sealing performance of EPDM gaskets. In high-temperature applications, it may be necessary to increase the compression percentage to compensate for thermal expansion and maintain a tight seal.
5. **Fluid or Gas Type:** The type of fluid or gas being sealed can also influence the required compression. Aggressive chemicals or gases may require higher compression to prevent leakage and ensure compatibility with the EPDM material.
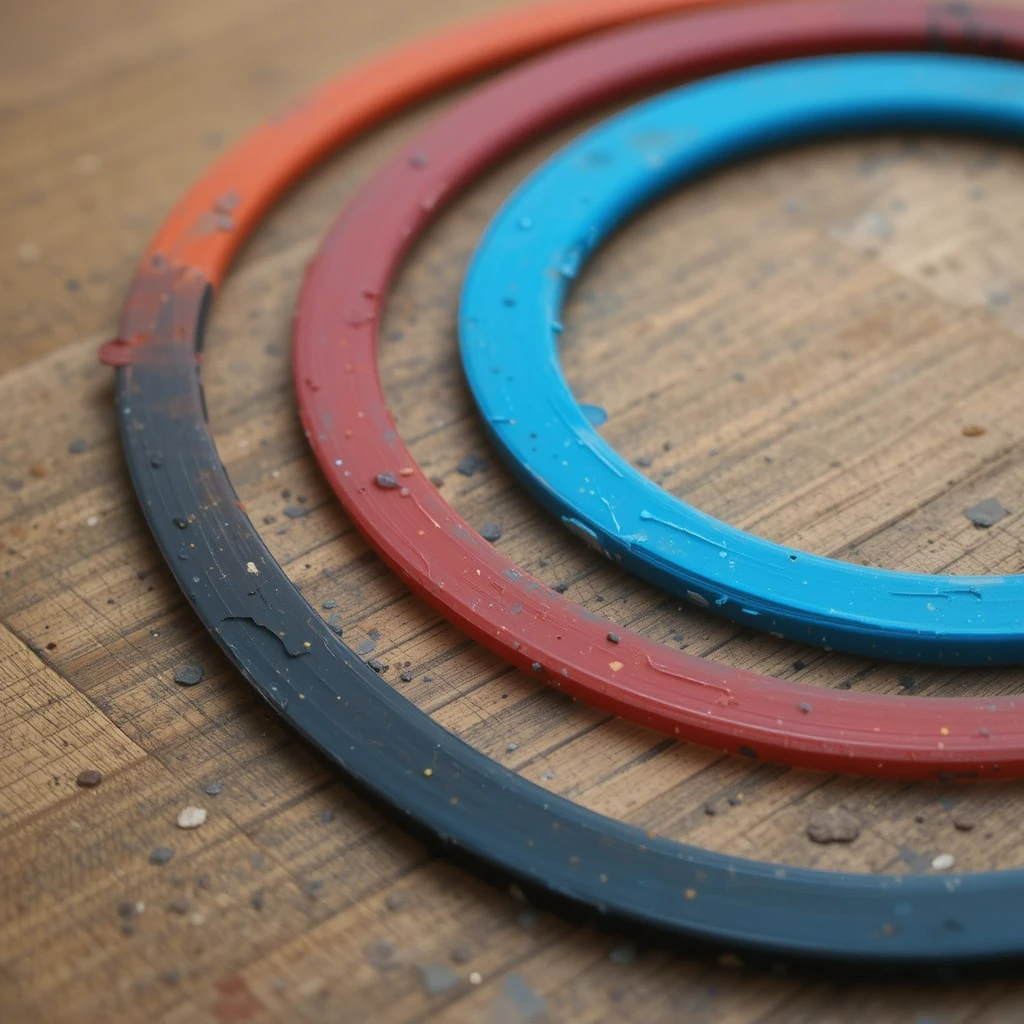
Determining Optimal Compression Percentage
The optimal compression percentage for EPDM gaskets can be determined through a combination of factors:
1. **Manufacturer Recommendations:** Always consult the gasket manufacturer’s specifications and recommendations for the specific EPDM gasket being used.
2. **Industry Standards:** Adhere to relevant industry standards and guidelines, such as those provided by ASME, ASTM, or other organizations.
3. **Testing and Validation:** Conduct testing and validation to verify the sealing performance of the gasket at different compression percentages under the specific application conditions.
4. **Experience and Expertise:** Leverage the experience and expertise of engineers and sealing specialists to determine the appropriate compression percentage based on the application requirements.
Conclusion
In conclusion, the compression percentage of EPDM gaskets is a critical parameter that significantly affects their sealing performance, lifespan, and overall reliability. By understanding the factors that influence optimal compression and following manufacturer recommendations and industry best practices, engineers and technicians can ensure that EPDM gaskets are properly installed and perform as intended, preventing leaks and maintaining system integrity.