Introduction
Ethylene Propylene Diene Monomer (EPDM) is a synthetic elastomer known for its exceptional resistance to weathering, ozone, and a wide range of chemicals. Consequently, EPDM gaskets are frequently employed in a diverse array of sealing applications across various industries, including automotive, construction, HVAC, and chemical processing. This document provides a comprehensive specification for EPDM gaskets, encompassing key properties, temperature range considerations, and chemical resistance characteristics.
1. EPDM Gasket Temperature Range.
EPDM gaskets exhibit excellent thermal stability and can withstand a wide range of temperatures. The typical operating temperature range for EPDM gaskets is -50°C to +150°C (-58°F to +302°F). However, the actual temperature range may vary depending on the specific EPDM formulation and the application. Typically, a company that offers customers a specific solution will provide detailed information about the rubber specifications they are offering. For example:
EPDM 3mm gaskets – Custom Made
Low-Temperature Performance:
EPDM remains flexible and resilient at low temperatures, making it suitable for applications in cold climates or cryogenic environments. However, at extremely low temperatures, the material may become brittle.
High-Temperature Performance:
EPDM can withstand continuous exposure to elevated temperatures without significant degradation. However, prolonged exposure to temperatures above 150°C (302°F) may lead to hardening, cracking, and loss of elasticity.
Temperature Cycling:
EPDM gaskets can withstand repeated temperature cycling without significant deterioration. However, rapid temperature changes can induce thermal stress, which may affect the gasket’s sealing performance.
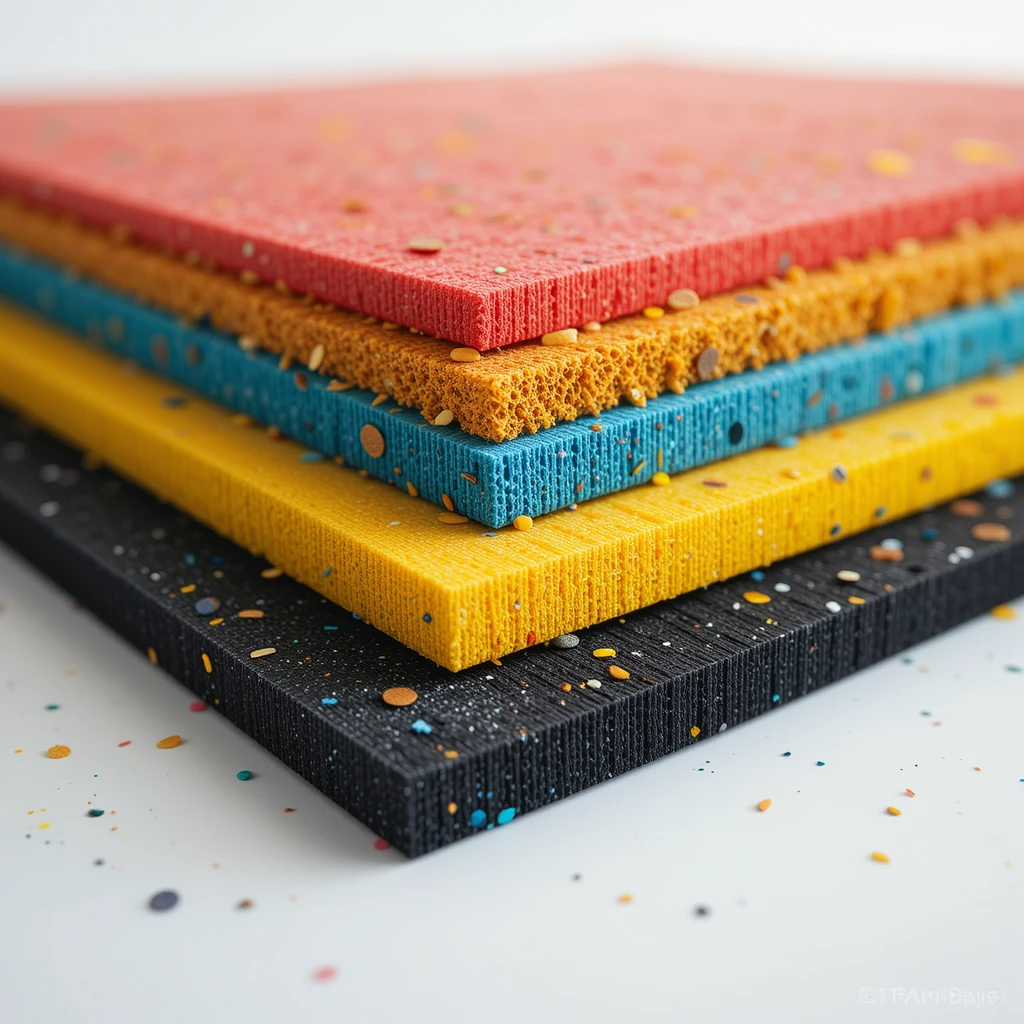
2. EPDM Gasket Chemical Resistance
EPDM is renowned for its exceptional resistance to a broad spectrum of chemicals, making it a versatile sealing material for various industrial applications. Its chemical resistance profile includes:
Excellent Resistance:
Water and Steam: EPDM exhibits excellent resistance to water and steam, making it ideal for sealing applications in plumbing, HVAC, and steam systems.
* Ozone and Weathering: EPDM is highly resistant to ozone degradation and weathering, making it suitable for outdoor applications.
* Dilute Acids and Alkalis: EPDM can withstand exposure to dilute acids and alkalis without significant degradation.
* Alcohols: EPDM demonstrates good resistance to alcohols, making it suitable for applications involving alcoholic beverages or solvents.
* Ketones: EPDM generally exhibits good resistance to ketones.
* Glycols: EPDM is compatible with glycols, commonly used in antifreeze and heat transfer fluids.
* Phosphate Esters: EPDM shows reasonable resistance to phosphate ester-based hydraulic fluids.
Moderate Resistance:
Concentrated Acids and Alkalis: Exposure to concentrated acids and alkalis may cause swelling and degradation of EPDM.
* Vegetable Oils: Prolonged exposure to vegetable oils may lead to swelling and softening of EPDM.
* Some Solvents: Resistance to solvents varies depending on the specific solvent and EPDM formulation. A compatibility chart should be consulted.
Poor Resistance:
Petroleum-Based Oils and Fuels: EPDM is not recommended for use with petroleum-based oils and fuels, as it can swell and degrade rapidly.
* Aromatic Hydrocarbons: Aromatic hydrocarbons such as benzene and toluene can cause significant swelling and degradation of EPDM.
* Chlorinated Solvents: Chlorinated solvents such as methylene chloride and trichloroethylene are incompatible with EPDM.
3. EPDM Gasket Physical and Mechanical Properties
The physical and mechanical properties of EPDM gaskets are critical for ensuring reliable sealing performance. Key properties include:
Hardness:
Measured using a durometer, hardness indicates the gasket’s resistance to indentation. Typical EPDM gasket hardness ranges from 40 to 90 Shore A, depending on the application.
Tensile Strength:
Tensile strength represents the maximum stress the gasket can withstand before breaking under tension. Higher tensile strength indicates greater resistance to tearing and deformation.
Elongation at Break:
Elongation at break measures the percentage of elongation the gasket can undergo before fracturing. High elongation at break allows the gasket to conform to irregular surfaces and maintain a tight seal under stress.
Compression Set:
Compression set is a measure of the gasket’s ability to recover its original thickness after being subjected to compressive force for a specific period at a given temperature. Low compression set is essential for maintaining a long-term seal.
Tensile Modulus:
The tensile modulus is a measure of a material’s stiffness or resistance to deformation under tensile stress.
Tear Resistance:
Tear resistance indicates the material’s ability to resist tearing, which is particularly important for gaskets subjected to high stress or abrasion.
Density:
The density of the EPDM compound can influence its weight and suitability for specific applications.
4. Standards and Specifications
EPDM gaskets are often manufactured to meet specific industry standards and specifications. Common standards include:
ASTM D2000:
This standard classifies rubber materials based on their physical properties and chemical resistance. EPDM materials are typically classified under this standard.
SAE J200:
This standard specifies requirements for rubber parts used in automotive applications.
NSF/ANSI 61:
This standard certifies that the EPDM material is safe for use in contact with drinking water.
FDA 21 CFR 177.2600:
This regulation specifies requirements for rubber articles intended for repeated use in contact with food.
EN 681-1:
This European standard specifies requirements for sealing materials used in water supply and drainage applications.
5. EPDM Gasket Selection Considerations
When selecting an EPDM gasket for a specific application, it is essential to consider the following factors: Application Requirements:
The specific application requirements, including temperature range, chemical exposure, pressure, and sealing requirements, should be carefully evaluated.
EPDM Compound Formulation:
The EPDM compound formulation should be selected to meet the specific application requirements.
Gasket Dimensions and Tolerances: The gasket dimensions and tolerances should be carefully specified to ensure a proper fit and reliable sealing performance.
Industry Standards and Specifications:
The gasket should comply with relevant industry standards and specifications.
Supplier Reputation and Experience:
The gasket supplier should have a proven track record of providing high-quality EPDM gaskets.
6. EPDM Gasket Composition and Manufacturing
EPDM gaskets are typically manufactured through compression molding, injection molding, or extrusion processes. The specific formulation of the EPDM compound can be tailored to meet specific application requirements. Key components of a typical EPDM gasket formulation include:
EPDM Polymer:
The base polymer provides the inherent elastomeric properties and resistance to degradation. Different grades of EPDM polymer are available, each offering specific performance characteristics.
Fillers:
Fillers such as carbon black, clay, or silica are added to enhance mechanical properties, improve processing, and reduce cost. The type and quantity of filler significantly influence the gasket’s hardness, tensile strength, and elongation at break.
Plasticizers:
Plasticizers are incorporated to improve flexibility, processability, and low-temperature performance.
Curing Agents:
Curing agents, typically sulfur-based or peroxide-based systems, facilitate the crosslinking of the EPDM polymer chains, resulting in a thermoset material with enhanced strength and elasticity.
Processing Aids:
Processing aids such as lubricants and dispersing agents are added to improve the flow and mixing of the compound during manufacturing.
Stabilizers and Antioxidants:
Stabilizers and antioxidants are crucial for protecting the EPDM material from degradation caused by heat, oxygen, and UV radiation.
Conclusion
EPDM gaskets are a versatile and reliable sealing solution for a wide range of applications. Their excellent resistance to weathering, ozone, and various chemicals, combined with their broad temperature range, makes them a preferred choice for demanding environments. By carefully considering the factors outlined in this specification, engineers and designers can select and implement EPDM gaskets that provide long-lasting and dependable sealing performance. It is crucial to consult with EPDM gasket manufacturers and suppliers to ensure the selection of the appropriate compound and design for each specific application. Regular inspection and maintenance are also essential for maximizing the lifespan and performance of EPDM gaskets.