Introduction
The selection of an appropriate rubber gasket material is a critical decision in engineering design and maintenance, directly influencing the long-term performance and reliability of sealed systems. A comprehensive understanding of the application’s operational parameters, environmental conditions, and regulatory compliance requirements is paramount to ensuring optimal gasket functionality. Many companies which are offering gasket cutting services for example https://csmade.co.uk/ can help with material choice. This discussion will outline key considerations for choosing rubber gasket materials, emphasizing the importance of matching material properties to specific application demands.
Material choice
Firstly, consider the chemical compatibility of the rubber material with the fluids or gases it will be exposed to. Different rubber compounds exhibit varying levels of resistance to different chemicals. For example, nitrile rubber (NBR) demonstrates excellent resistance to oils, fuels, and hydraulic fluids, making it a suitable choice for automotive and industrial applications involving these substances. However, NBR is not ideal for applications involving ozone, ketones, or esters. Conversely, fluorocarbon elastomers like Viton (FKM) offer superior resistance to a broad range of aggressive chemicals, including acids, bases, and solvents, making them suitable for demanding chemical processing environments. It is crucial to consult chemical resistance charts and conduct compatibility testing to ensure the chosen material will not degrade or swell upon exposure to the intended media, which could compromise the seal’s integrity.
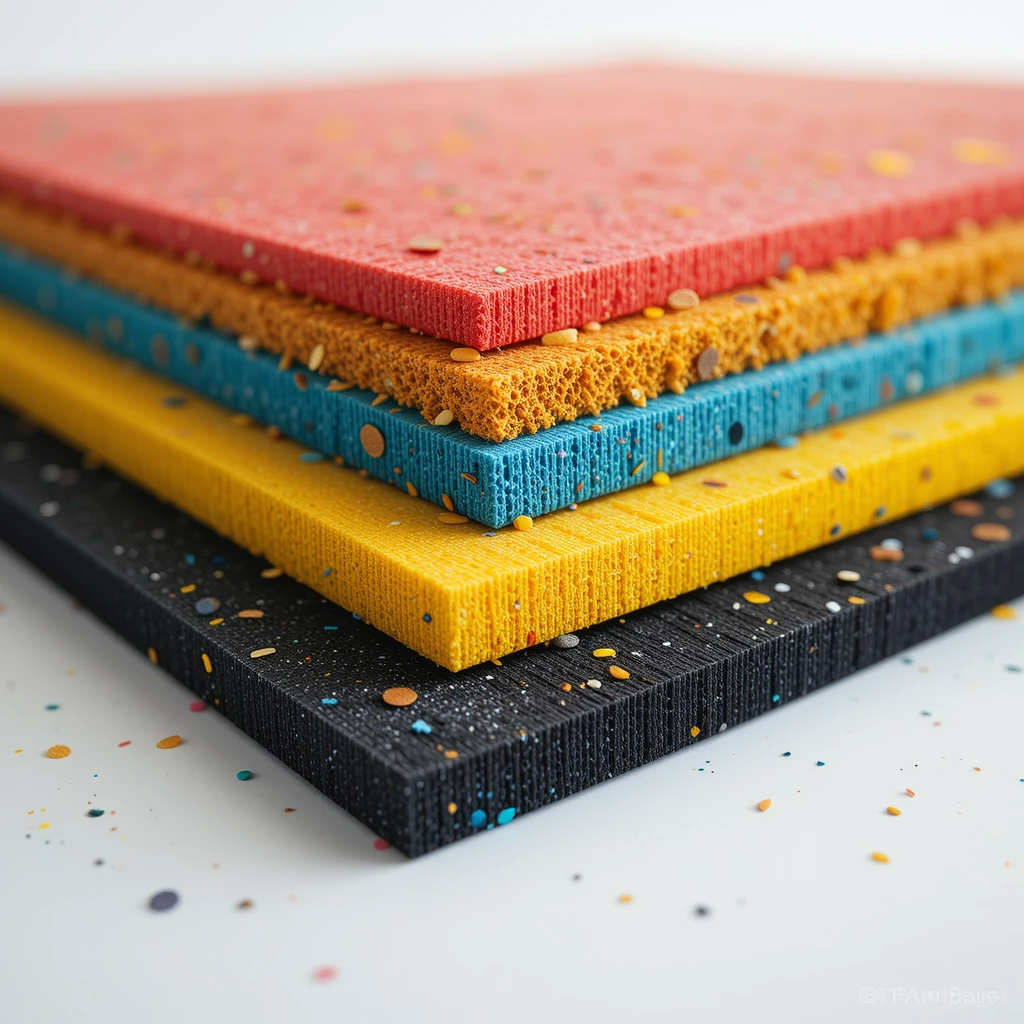
Temperature specification
Secondly, temperature is a significant factor influencing rubber gasket performance. Each rubber compound has a defined operating temperature range. Exceeding these limits can lead to hardening, cracking, or softening of the material, resulting in leakage. Silicone rubber (VMQ) and fluorosilicone rubber (FVMQ) excel in both high and low-temperature environments, making them suitable for aerospace, automotive, and food processing applications where temperature extremes are prevalent. Ethylene propylene diene monomer (EPDM) rubber offers good heat resistance and excellent weathering properties, making it a viable choice for outdoor applications. Careful consideration of the application’s temperature profile, including potential temperature spikes, is crucial for selecting a material that will maintain its elasticity and sealing properties.
Mechanical properties
Thirdly, mechanical properties such as tensile strength, elongation, and compression set must be considered. Tensile strength refers to the material’s ability to withstand stretching forces, while elongation measures its ability to stretch before breaking. Compression set is a measure of the material’s permanent deformation after being subjected to a compressive load over a period of time. A low compression set is desirable, as it indicates the gasket will retain its original shape and sealing force. For applications involving high pressures or dynamic loading, materials with high tensile strength and low compression set, such as hydrogenated nitrile rubber (HNBR) or fluorocarbon elastomers, are often preferred.
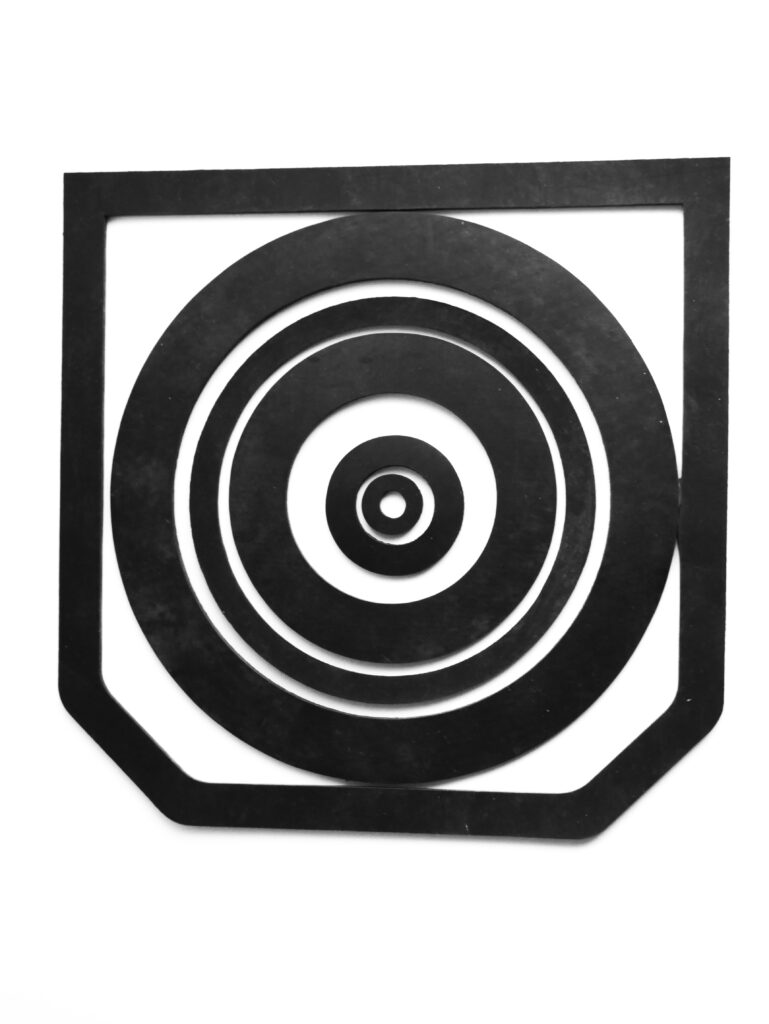
Environmental factors
Furthermore, environmental factors beyond temperature and chemical exposure must be taken into account. Exposure to ozone, ultraviolet (UV) radiation, and weathering can degrade certain rubber materials over time. EPDM rubber exhibits excellent resistance to ozone and weathering, making it a good choice for outdoor applications. The presence of abrasive particles or the potential for mechanical abrasion can also impact gasket life. In such cases, materials with high abrasion resistance, such as polyurethane rubber, may be considered.
Regulatory compliance
Finally, regulatory compliance requirements must be met. For applications in the food, pharmaceutical, and medical industries, gasket materials must comply with standards such as FDA regulations, USP Class VI, and NSF certifications. These standards ensure the materials are non-toxic and will not leach harmful substances into the process stream.
Conclusion
In conclusion, selecting the appropriate rubber gasket material requires a thorough evaluation of the application’s specific requirements. Chemical compatibility, temperature range, mechanical properties, environmental factors, and regulatory compliance are all critical considerations that must be carefully assessed to ensure long-term sealing performance and system reliability. Consulting with material suppliers and conducting thorough testing are essential steps in the selection process.